The machinery used in the construction of a building project is called construction equipment, whose components mainly consist of drivetrains, chassis frames, jibs and etc. They are essential to ensure the equipment function and durability.
For the architectural equipment, metal parts machining in CNC precision technology is advantaged in high precision and efficiency. Tight tolerances and outstanding surface quality can be achieved, assuring the reliability and performance of construction equipment.
Table of Contents
Machining Drivetrain Components in High Efficiency
Transmissions are very essential to construction equipment such as lifts, excavators and cranes. While the manufacturing of components faces some challenges, including machining the tooth shape of gears and the internal structure of bearing housings. And the transmission system components usually need to be strictly fitted, such as gear meshing clearance, bearing assembly clearance, etc.
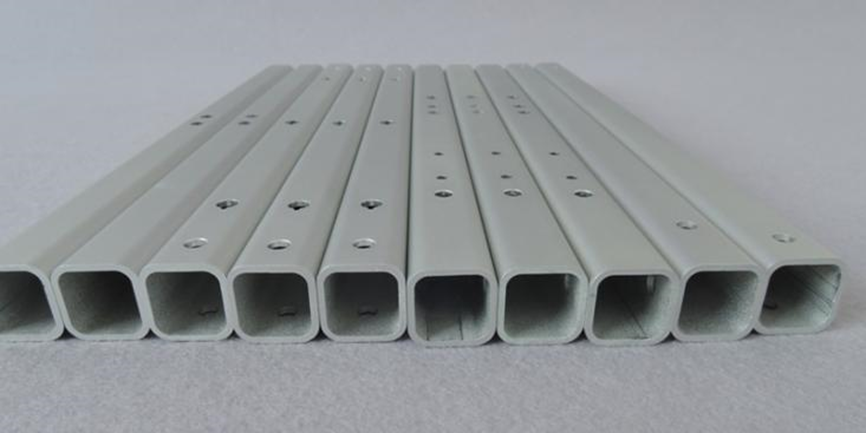
These require high-precision CNC machining techniques to ensure the quality and performance. In addition, drivetrain systems are often subjected to high operating loads and vibration. So the surface quality and strength of drivetrain components are also machining difficulties.
High-precision CNC machine tools are operated by computerized numerical control (CNC) systems, which are able to precisely cut, drill and shape. CNC systems are capable of handling complex programming instructions and executing high-precision tool paths to ensure precision in part geometry and dimensions. For example, CNC machines can achieve ±0.05mm machining accuracy, which can meet the tight tolerances required for high-precision gears, bearings and other critical components in the transmission system.
CNC machines can achieve high consistency in machining multiple parts, which ensures that each part meets the design specifications. The geometry of transmission components is often complex, such as helical and non-circular gears. High-precision CNC machines can process complex surfaces through multi-axis linkage technology. And the trajectory of the tool can be precisely controlled to process complex shape structures.
CNC machining can accurately remove the amount of material , to achieve the required size and surface finish of critical components, such as bearings and couplings. Meanwhile, CNC machines are equipped with a variety of sensors and monitoring systems to monitor the machining process in real time, such as tool position, cutting force and temperature. Once any parameter abnormality is detected, the system can immediately make adjustments to ensure machining accuracy.
Machining Crane Chassis Frames With High-precision
Cranes are used for lifting and conveying materials in different circumstances. The crane chassis mainly involves a base, supporting part and fixing bolts. The base is stable to bear loading, and the support part is composed of steel tubes or steel plates. The fixing bolts secure the base to the ground, ensuring that the chassis is firm in usage.
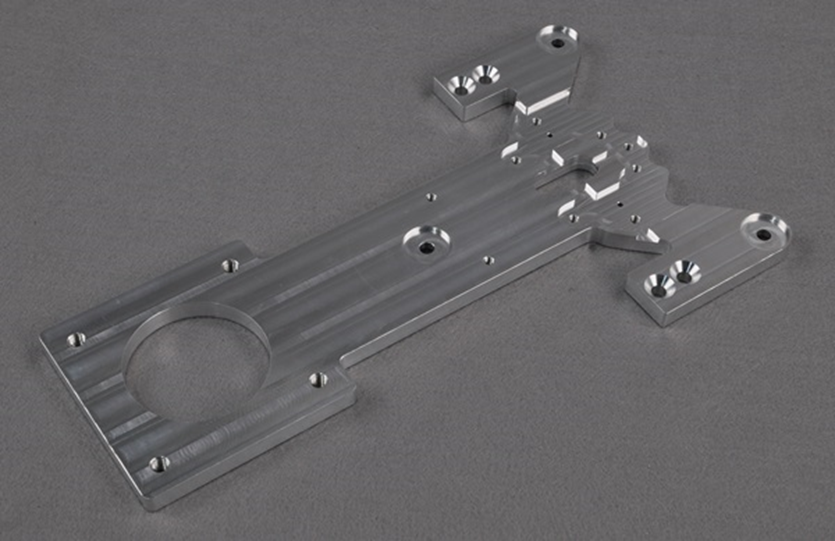
CNC machine used in processing crane chassis can flexibly change the milling cutter according to the milling demands. Its movement trajectory and working parameters can be controlled through the computer to achieve high-precision machining, which improves the stability and productivity of the chassis. The metal parts machining is highly repeatable, and great processing accuracy can greatly assure the quality and safety of the crane chassis.
For the specific shape and size of the chassis, special fixtures and jigs are designed to ensure stable fixation and precise positioning of the parts during machining. The fixtures should have sufficient strength and rigidity, and at the same time consider the convenient clamping and adjustment functions. In addition, the thermal deformation compensation of the CNC system can monitor the temperature changes during machining. The machine parameters are then automatically adjusted to compensate for dimensional errors due to thermal deformation.
Boom Truck Structures Machining
Boom is the main functional part of the crane system operation, generally including the main boom and jib two parts. There are two main types of main boom of crane, one is truss structure boom and the other is box structure boom with various sections. With the development of truck cranes, most of the main boom of truck cranes are box structure now.
CNC machine tools have a variety of machining functions, such as milling and turning. They can handle complex curved surfaces and large-size parts. Through the coordinated movement of multiple axes, the entire machining area of the boom can be effectively covered, reducing the errors caused by multiple clamping. Disassembly machining can also be used. It disassemble large parts into several parts in design. Separate parts are machined and then glued or welded together.
Choosing high-performance tools with high-strength materials to machine boom parts, such as coated carbide tools or ceramic tools, can improve cutting efficiency and tool life. At the same time, use a high-efficiency coolant system to reduce the temperature in the machining area and minimize thermal deformation and tool wear.
Set appropriate cutting speed, feed rate and depth of cut, which optimize the cutting path and reduce cutting force and heat generation. Adopt step-by-step roughing and finishing methods to gradually approach the final size and reduce the impact of single machining on the part.
CNC Automated Production of Gearboxes
Transmission is a mechanical device used to control the output speed of the motor to regulate the motor output power and characteristics. It has the function of variable speed ratio and changing gears, etc. It can adjust the output speed of the crane according to the change of the load, and get a better running effect. In addition, the transmission can also effectively increase the crane running speed to better meet the work requirements.
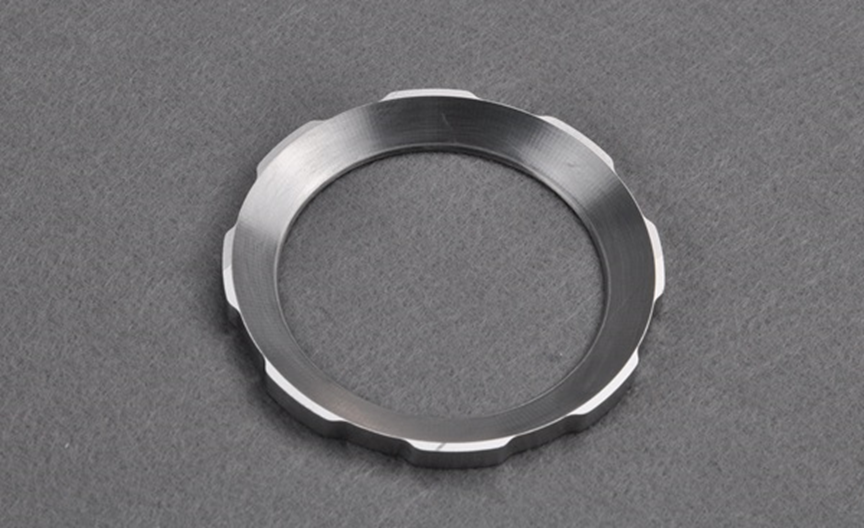
If the machined parts are not precise enough, it may lead to the paralysis of the whole transmission system. The processing of the transmission is more complicated, and it is more difficult to ensure precision. General way of processing is often used in three sequences. The first sequence and the second sequence of standard hydraulic chuck and top of a clip a top way to carry out both ends of the semi-finish car, the third sequence of two top clamps top tight way to carry out the finish car.
CNC machine center can process precision transmission parts and components, as well as carry out mass production to achieve high degree of automation of the CNC metal parts machining, which reduces manual intervention and operation. Automated CNC production greatly shortens the production cycle of gearboxes, saves total costs and improves production efficiency.
Conclusion
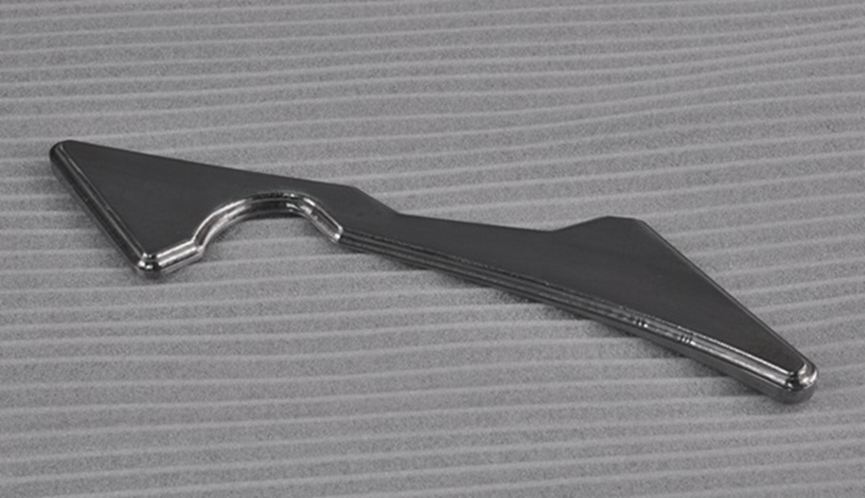
CNC precision machining technology can efficiently process construction equipment parts. Also the accuracy and stability of metal parts machining can be guaranteed. At present, there are high initial investment and high technical requirements for CNC precision technology. However, to realize the mechanical automation production for construction industry, the promotion of CNC precise machining technology has been an inevitable trend.